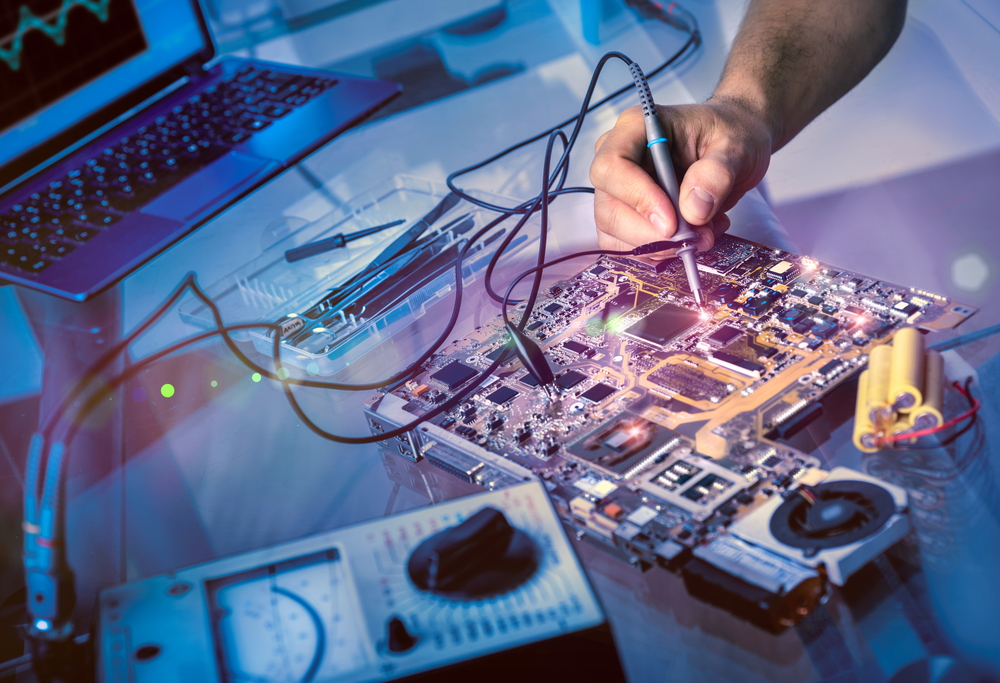
Hoe maak je een design first time right: “De oplossing is altijd procesmatig”
De snelle technologische vooruitgang en stijgende vraag naar elektronica plaatst de elektronicasector voor grote uitdagingen. Want hoe kan je in een wereld van componenten- en personeelsschaarste de time-to-market verkorten, de productie verhogen en tegelijk voldoen aan de steeds strengere technische eisen van de klant? Right first time, een werkwijze waarbij een product in één keer foutloos de fabriek uitrolt, lijkt niet langer een optie maar een must. Dick van Hees (MRMc) en Ruud van Beek (ASML) delen tijdens de plenaire lezing op het D&E event hun ervaringen met right first time en durven daarbij de pijnpunten te benoemen.
We spreken met Ruud van Beek, Technical Supplier Manager Electronics bij ASML. Hij stond samen met zijn collega Dick van Hees twaalf jaar geleden aan de wieg van de mentaliteitsomslag bij de Nederlandse techreus die leidde tot de right first time-werkwijze. Een methode die toen nog vrij nieuw en onbekend was in ons land. Van Beek: “Vijftien jaar geleden kochten we componenten extern in en zetten we het vervolgens zelf in elkaar. De failure rate was enorm hoog, op het dieptepunt zelfs rond de 60%. Het was duidelijk dat het zo niet langer ging. Daarom hebben we het roer compleet omgegooid; van plug ’n pray naar plug ’n play”.
Weerstand
“Bij right first time gaat het erom dat je producten levert aan de klant die direct van uitstekende kwaliteit zijn, dus met een zeer laag foutenpercentage. Dit lukt alleen als je leveranciers en ontwerpers vanaf dag één bij een project betrekt,” vervolgt Van Beek. In de praktijk bleek dit makkelijker gezegd dan gedaan. “Toen we hier twaalf jaar geleden mee aan de slag gingen, kregen we te maken met weerstand. Collega’s waren gewend aan een bepaalde werkwijze en wilden die niet zomaar veranderen. We moesten ze overtuigen door de voordelen die right first time oplevert voor onze klanten en ook voor onszelf duidelijk te maken. Het werkplezier neemt echt toe als je producten steeds beter worden”.
Ontevreden
Gepensioneerd ASML-er en adviseur Dick van Hees herinnert zich deze spannende periode nog als de dag van gisteren. “Uiteindelijk heb je als bedrijf alleen bestaansrecht als je klanten tevreden zijn en dat waren ze op dat moment niet. Daarom hebben we het direct groots aangepakt door een project op te zetten met drie OEM-ers uit de omgeving en zeventien van onze gezamenlijke maakbedrijven”.
Het projectteam schakelde de hulp in van onafhankelijke onderzoeksbureaus, waaronder IMEC en TNO. Het doel was om een model te ontwikkelen waarmee het foutenpercentage voorspelt kon worden op basis van bestaande data. De overheid stelde subsidie beschikbaar en anderhalf jaar later was het model klaar. Van Hees: “Ik ben nog steeds trots op het resultaat, want het model betekende een enorme verbetering voor onze bedrijfsprocessen. Als je namelijk weet wat er in het verleden misging, kan je voorspellingen doen en maatregelen nemen om fouten in de toekomst te voorkomen.”
Makkelijk principe
“Het principe is eigenlijk heel makkelijk,” legt Van Hees uit “als je de onderdelen in een BOM (bill of materials) inzichtelijk maakt, kan je er de BOP (bill of process) uit genereren. Met data uit het verleden over de capability van een proces, kan je vervolgens voorspellen hoeveel producten zullen falen als ze afgeleverd worden. De volgende stap is om dit aantal omlaag te krijgen en daarvoor zijn verschillende oplossingen mogelijk.”
“Tijdens mijn presentatie geef ik een aantal praktijkvoorbeelden,” vervolgt Van Hees. “Stel, een monteur vergeet tijdens de productie een O-Ring waardoor een machine kan gaan lekken tijdens gebruik. Een mogelijke oplossing is dat je de benodigde O-ringen alleen beschikbaar stelt in de maakvolgorde (kitten). De eerste stap is altijd om te kijken of het ontwerp zodanig gemaakt kan worden dat er geen fout op kán treden. Stap twee is het proces zodanig inrichten dat het onmogelijk is om de fout te maken. Stap drie, die je eigenlijk liever niet wilt, is een test toevoegen die de fout opvangt voordat hij bij de klant komt. Al deze stappen besteden we uit aan onze partners, waardoor wij ons nog beter kunnen focussen op onze specialiteit: het maken van machines”.
Rond de tafel
Van Beek. “Het zijn vaak de kleine details die bepalen of een ontwerp geslaagd is. De klant interesseert het niet dat de oorzaak van het probleem een vergeten schroefje is. Het enige wat de klant wil, is dat de machine werkt. En dat is begrijpelijk, de nieuwste generatie chipmachines van ASML kosten meer dan 100 miljoen euro per stuk. Daarom kijken we continue hoe we onze bedrijfsprocessen verder kunnen optimaliseren en aanscherpen. Een ketting is zo sterk als de zwakste schakel en dat geldt ook voor onze machines”.
Closing the feedback
Tot slot speelt closing the feedback een belangrijke rol bij het verbeteren van de operationele processen binnen ASML. Van Beek: “Durf fouten uit het verleden onder ogen te zien en te verwerken in je ontwerp. Zo voorkom je dat je steeds dezelfde fouten maak”. Van Hees sluit zich aan bij zijn oud-collega: “Bij alles wat we ontwerpen stellen we de vraag: is het maakbaar, testbaar, eenduidig en compleet. Een bepaalde foutmarge is acceptabel voor de klant, bijvoorbeeld 1 op de 1000, maar dit moet je als bedrijf wel onderbouwen. Vaak zijn test- en ontwerpfouten het gevolg van kleine menselijke onvolkomenheden, maar uiteindelijk is de oplossing altijd procesmatig”.
Kom naar de lezing
Wil je meer te weten komen over de ervaringen en best practices van ASML met right first time? Kom dan naar de plenaire lezing van Dick van Hees en Ruud van Beek op het D&E event. De toegang voor de lezing en het event is kosteloos, maar je moet je wel van tevoren aanmelden via de website van het event. Tot ziens in Den Bosch!