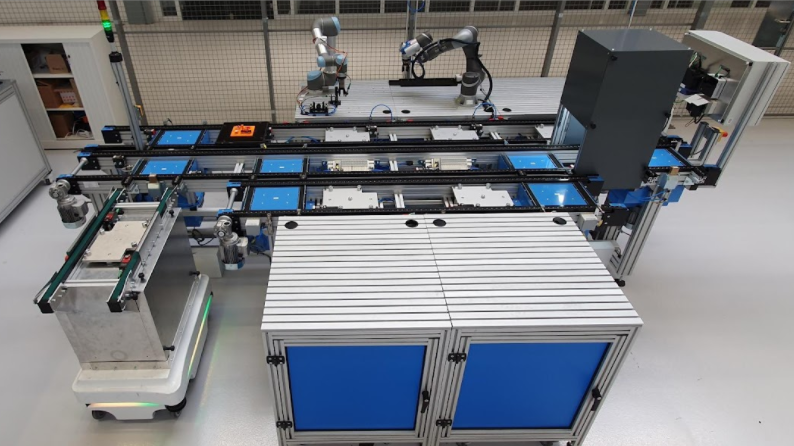
Fontys develops robot-controlled transfer system with IXON
Fontys is the largest University of Applied Sciences in the south of the Netherlands, with more than 25 separate institutes in 10 different cities. One of these is in Eindhoven, located at the high-tech manufacturing Brainport Industries Campus (BIC).
Here, a group of researchers, teachers, and students from Fontys University of Applied Sciences School of Engineering has developed a way to improve the efficiency of an already existing robot production line using the IXON Cloud and IXrouter. The solution: A robot-controlled transfer system for the manufacturing industry.
We talked to Randy Kerstjens, a lecturer-researcher Mechatronics and Robotics at Fontys, to find out more about the project and its real-life applications.
Could you give us a quick overview of your project?
The manufacturing industry is becoming increasingly automated and factories are growing smarter with robots executing tasks. We wanted to take it one step further.
Enter project FLUFFY; (the) FLexible aUtomated Future FactorY. We created a production line and then upgraded it by adding multiple robots that not only assemble parts but subsequently also place them in designated positions. This combination creates a more efficient, flexible production system to be used in the manufacturing industry for example.
“The innovative aspect here is the combination of robots that collaborate and can supply and move components or finished products to a transfer system with different workstations.”

Why did you choose to work with IXON?
When working on projects like these, the intention is always to have close collaboration with the professional field. For project FLUFFY, we needed a remote access solution that was easy to work with, a reliable bridge between students’ and teachers’ network activity - for collaboration during a time when we couldn’t necessarily meet in person.
I had used IXON in my own company Concept Robotics, and knew about the quick set-up, intuitive platform, and easy collaboration feature, so I reached out to see whether we could use their all-in-one IIoT platform for this project. They understand how supporting research projects like this one, enables us all to take part in shaping innovative solutions of the future, and IXON was happy to collaborate.
How did you test the concept?
For this project I worked with two students from the Adaptive Robotics minor within the Mechatronics department. The automated production system was developed and installed at the Brainport Industries Campus (BIC) in Eindhoven, where innovative, high-tech concepts for the manufacturing industry are created. The concept - from delivery of the individual parts, to assembly, and finally quality control - was to be tested on a Lego Formula 1 cart.
We built a small scale production line with several workstations and created a set-up, in which a toploader was mounted on an Autonomous Mobile Robot (AMR). The toploader would pick up the parts of the Lego Formula 1 cart from one workstation, and place them at the assembly station for a robot arm to assemble. This process was being monitored by a camera application, developed as part of another graduation project for quality control.
“If a mistake occurs in the production line, the camera catches it and sends the faulty part to a different production lane where it can be repaired.”
What part did IXON play?
In this case we used the IXON module as a remote access solution. We easily set up a VPN connection to our system and started remotely monitoring and - when necessary - debugging the system. The user management feature allowed us to add all project-participants to the platform and provide role-based access control. As a result, we were able to make changes remotely and efficiently collaborate with colleagues and students - whether they were working from home or on location.
In the near future, we are planning to implement data logging as well. This will make it possible to collect, monitor, and later analyze a variety of crucial data points for production optimization.

What are the real-life applications of this project?
Practice-oriented research like this gives students the opportunity to combine learning and working on projects that have a real, demonstrable impact on the professional field.
Within the manufacturing industry demand is increasingly growing for advanced systems that are more comprehensive and encompass a broader range of subsequent tasks. Our flexible robot assembly system could automate a large part of the assembly and manufacturing process of a variety of products, such as mobile phones, small (electronic) assemblies, pillboxes etc.
As a result, companies are looking at the new production line of the future; with added operational value like increased efficiency, more flexible production, and minimized human errors, as well as business value through new opportunities for collaborations within the manufacturing industry.
Sounds promising! What’s next?
Of course this is not the end of it. We are learning from new developments in the field and other research being conducted, implementing those learnings into our own project. This allows us to develop and improve FLUFFY, and continuously contribute to innovative solutions in the field - with strong partners like IXON by our side.